Mike Dean – Award Winning Wood Turner
Tommy wanted Mike to make some splindles for his staircase and as Tommy liked two of Mike’s designs so much he had Mike combined them onto one spindle – giving Tommy a totally unique design.
Another piece that Mike is especially pleased with is a 3ft bowl, which is now exhibited at the famous London restaurant La Tante Claire. The bowl was worked on while it was still wet; giving it a unique twisted and buckled shape.
Mike made a large handmade stand together with a decanter and six wooden goblets, presented to the Reverend Dr Canaan Banana from Zimbabwe.
Along the way Mike has collected many awards including both first and second in the 1995 British Gates and Timber Woodturning competition, third place at the 1996 Practical Wood turning Show at Wembley and one year later a second at the Good Woodworking Show at Alexandra Palace.
Mike has come a long way in a career spanning over 30 years – and to think it all started with a rabbit hutch he made with his father.
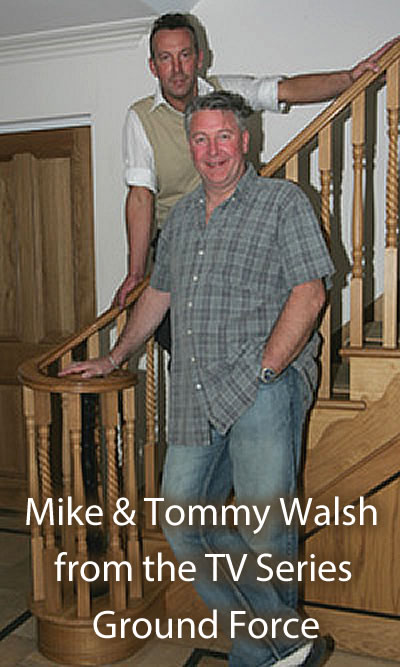
Woodturning Magazine Feature
Guest editor Dave Bates introduces woodturning all-rounder Mike Dean
I first met Mike Dean around 1998 when he started his woodturning business, Barleywood, near Hastings in East Sussex. Back then he had a new Hapfo copy lathe and two ‘hand’ lathes and my fist impression was that here was a man intent on working to succeed with an enthusiasm not unlike a pack of hounds fresh on the scent. Twenty-odd years later, the enthusiasm remains undimmed but the amount of machinery to create the huge range he sells has expanded to almost fill the workshop.
What I admire about Mike is not just his enthusiasm but the hours of sheer graft he puts into filling orders and the huge range he covers, from architectural to artistic turning. We have kept in touch over the years – mainly when I refer enquiries for tens, hundreds or maybe thousands of a turned item – and he still hasn’t bought me a beer.
In his workshop now, along with the standard machines such as bandsaw, planer, sawbench etc., the Hapfo lathe has been extended to take 4m newel posts and columns, there is a second copy lathe, a barley twist machine, a CNC four blade planer (for preparing dowel blanks), a dowel cutter and separate dowel sander – and now three hand lathes.
His list of famous clients is impressive and among his portfolio of production turnings are literally tens of thousands of ballet barres which are exported to the US, Europe, Australia and Asia, marquee poles and dowels from 19-65mm, barley twist spindles, harp frames, porch columns up to 300mm diameter and a whole range of urns, #nials, knobs and suchlike. As he says, the production work pays the bills and allows him the time to indulge his passion for woodturning.
The workshop is an organised chaos of materials, #nished spindles and dowels ready to ship out, a personal squirrel-hoard of oak and elm burrs and, on most free flat surfaces, an eclectic mix of bowls, vases and dishes that would grace any gallery.
Many woodturners like to augment their hobby by selling their work and a few dream of making a living at it. In this sense, Mike is living the dream and must be one of the very, very few making a good living from both production and artistic work alone, but the reality is hours and hours of driven work and to sum up his philosophy: Never miss an opportunity or turn a job down (no pun intended), market yourself, treat clients as you would wish to be treated and price jobs realistically.
It was a privilege to be given a tour of his workshop, to be privy to the details of his production work but above all, as a turner, to handle and drool over the shape and form of his freehand turnings. A browse of his website is a feast for the eyes:
Tell us about your background and training.
My first memory of woodworking goes back to when I was aged five and my father bought me a tool kit to make a rabbit hutch and, later, a go-kart.
On leaving school, I started on a youth training scheme making cabinets and staircases, then moved to a joinery !rm making windows, doors and conservatories.
Three years later, a job for a woodturner came up on a local paper and I have never looked back.
Creative Timber in Hastings then offered me a job making components for its #rniture range, including twisted columns, table legs and fluted spindles.
While I was working at Creative Timber I found a workshop available for rent which was already kitted out with planer, saw bench and crosscut and I thought this was an opportunity to start my own business. This was in July 1998. Sometimes you have to take a gamble in life and am so pleased I did.
How do you like to work, what are your favourite tools and why?
My favourite tool to use is a 1in special roughing gouge purchased from Jerry Glaser in the US. This is a very versatile tool, keeps it edge for ages and is a joy to use.
Describe your workshop – what is the set-up and how long have you been there?
My workshop is 1,500sq $ converted from a farm building and prior to 1998 was occupied by a joinery company, hence the machines I started with.
How does your design process work?
With my job you never know what is coming through the door. It could be wooden handles, stair parts, ballet barres, marque poles – anything that is round I can make. One of my favourite jobs to make is wooden porch columns because they need a little bit of thinking about and look stunning when finished. I have made these up to 300mm diameter and 2,500mm long.
Which woods do you most like working with and why?
For production work I like working with tulipwood (Liriodendron tulipifera, not Brazilian), which is easy to turn and !nish and is very stable. Burr elm and burr oak are my favourite woods to use for the artistic pieces I make, like thin delicate bowls and pieces that are turned green and le$ to dry naturally.
I have been using some burr horse chestnut recently and been trying deferent colours and finishes to produce the best possible results. I never work in any material except timber.
What sort of Finishes do you prefer and why?
Danish oil is my favourite !nish to bring out the natural beauty in the wood, but I do use sanding sealers and lacquers too, but these are more time consuming.
What inspires you and where do you get your ideas from?
Making thin, delicate bowls is my biggest passion and I was very lucky to have the late Bert Marsh in my workshop one Sunday to give a one-to-one lesson on how he made his delicate bowls. That gave me the inspiration to make these type of pieces. I have six of his pieces in pride of place in my office to keep looking at to give me design ideas [pic 10].
What is your favourite piece you have worked on and why?
My favourite piece was a stunning 36in-diameter burr oak bowl that was turned green and le$ to dry naturally.
What I like about such pieces is how they form a shape that cannot be repeated, a one-o%, and I was fortunate to have this [pic 1] purchased by a well-known chef in London.
What is the most challenging piece you have worked on, and why?
The most challenging piece I worked on was a hollow yew vase that was 28in high and 17in diameter. Mounting the piece on my VB36 and hollowing it to an even thickness then finishing took much longer than I had imagined [I know, I thought you never would – DB], but I kept going and was very pleased with result.
That’s one thing I have learnt in life; it doesn’t matter how difficult and challenging it can be at times, keep going and be positive.
How have the Covid-19 pandemic and lockdowns affected your work, and do you think any of the impact will be long term?
The pandemic did not really affect me too much and some parts of my work got busier because it gave people something to do at home. I am naturally an optimist so just work at my business and keep working as the jobs come in.
What are your aspirations for the future?
I want to carry on enjoying my work, meeting deferent people and be proud of what I have done and achieved.
What do you do when you’re not woodturning?
People ask what I do to switch off from work and relax. Turn bowls is the answer, but I do enjoy golf and fishing.
Google Reviews
Below are a collection of 5 star Google reviews from my many satisfied customers.
Contacted Mike at Barley Wood to make a porch column with some turning. All I gave him was a photo of something I quite liked that I had seen on the internet and some discretion based on his experience and knowledge.
We got progress photos and were able to add a little more turning. From order to delivery was two weeks. Very pleased with the finished porch column will be a real feature. Would recommend Mike and Barley Wood.
First class woodturner. He has done all our specialist wood turning for several years.
Mike was excellent from the initial phone call to the delivery of the finished goods. Perfect craftsmanship and professionalism. Thank you.
Classy work from a master craftsman. A really good service. Give Mike Dean a call you won't be disappointed.
Nice and helpful
Please Get in Touch
You can call us on 01424752000,
or fill in our contact form.
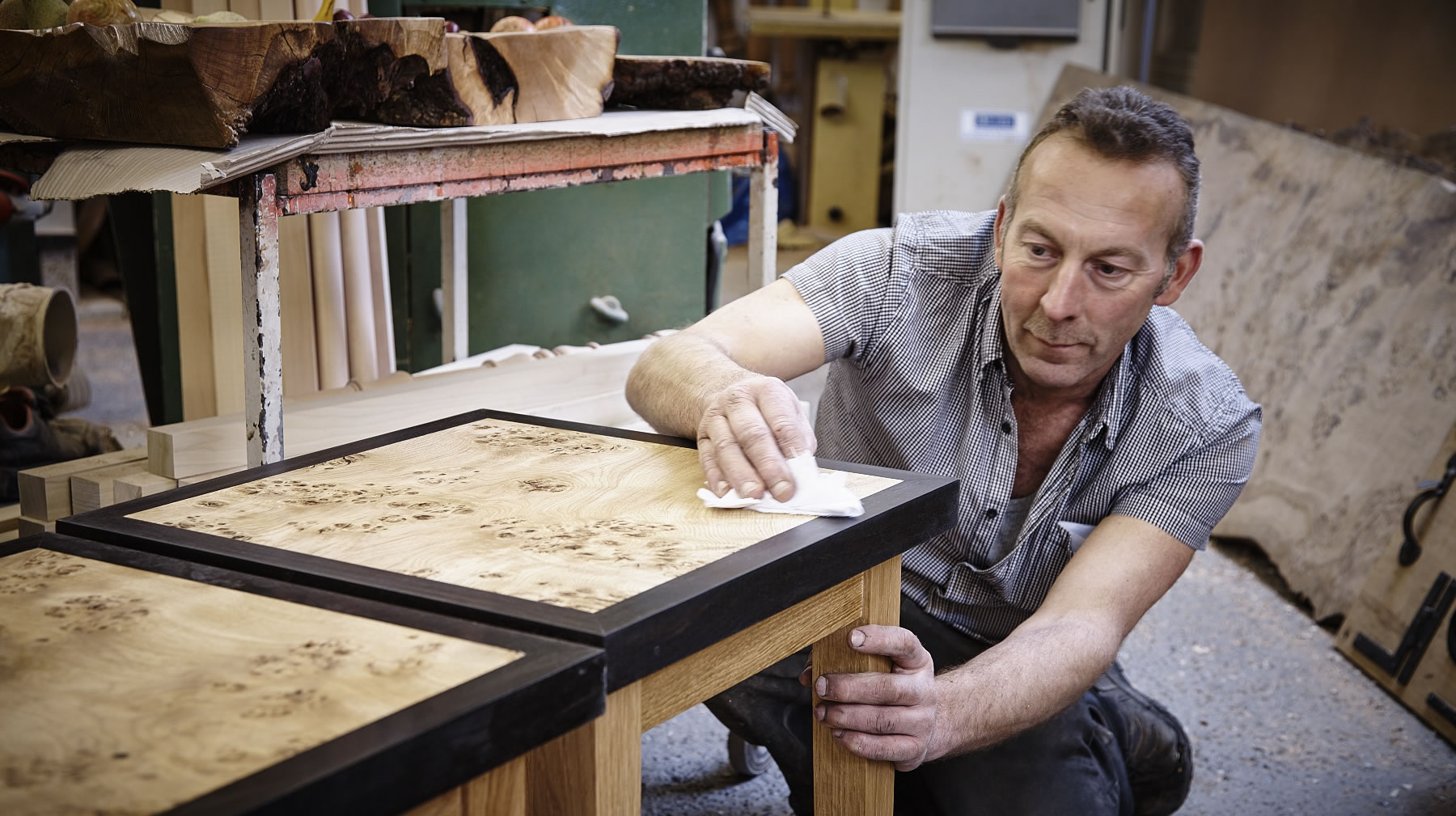